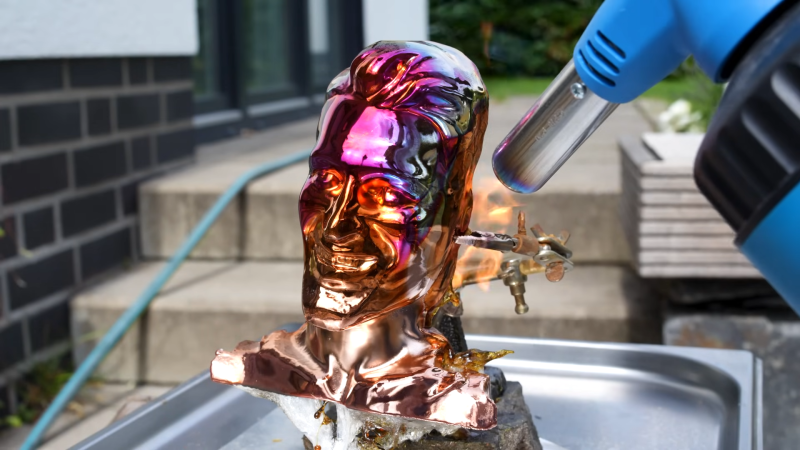
What if you electroplated a plastic 3D print, and then melted off the plastic to leave just the metal behind? [HEN3DRIK] has been experimenting with just such a process, with some impressive results.
For this work, [HEN3DRIK] prints objects in a special PVB “casting filament” which has some useful properties. It can be smoothed with isopropanol, and it’s also intended to be burnt off when used in casting processes. Once the prints come off the printer, [HEN3DRIK] runs a vapor polishing process to improve the surface finish, and then coats the print with copper paint to make the plastic conductive on the surface. From there, the parts are electroplated with copper to create a shiny metallic surface approximately 240 micrometers thick. The final step was to blowtorch out the casting filament to leave behind just a metal shell. The only problem is that all the fire tends to leave an ugly oxide layer on the copper parts, so there’s some finishing work to be done to get them looking shiny again.
We’ve featured [HEN3DRIK]’s work before, particularly involving his creation of electroplated 3D prints with mirror finishes. That might be a great place to start your research if you’re interested in this new work. Video after the break.
From Blog – Hackaday via this RSS feed